Alvis Cars - a Tour of the Fascinating Red Triangle
- aaronhussain440
- Jan 2, 2023
- 5 min read
Updated: Jan 3, 2023
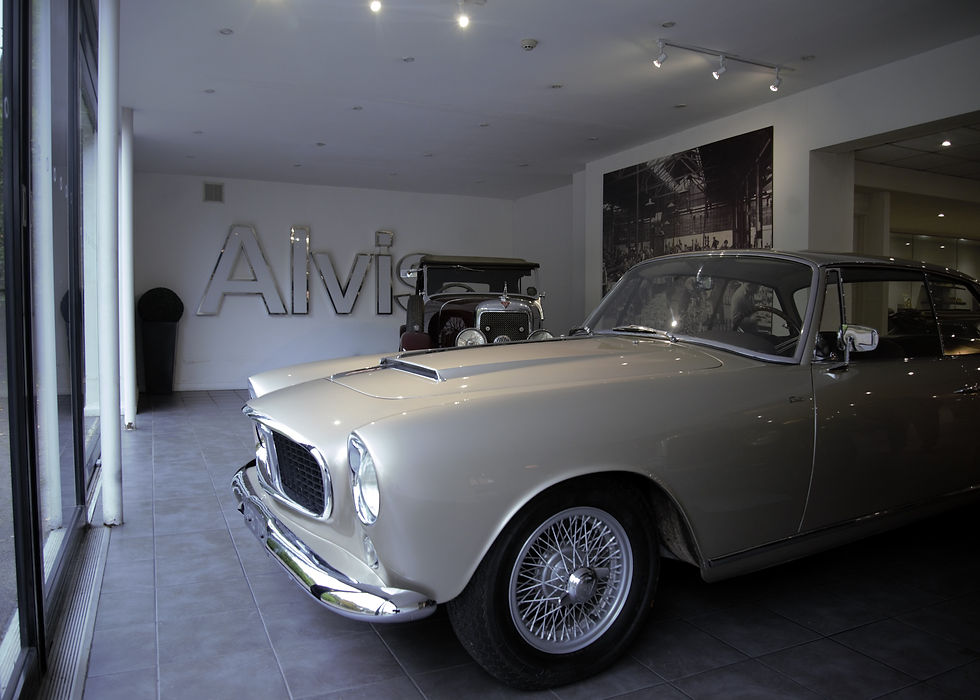
On Holyhead Road in Coventry, you might be tempted to stop to feast up on some fast food or go shopping for some new furniture without really giving it a second thought. But this being Coventry, the name of the retail park gives a clue as to what used to stand in its place: Alvis.
After Alvis car production ended in 1967, all the parts, expertise and a number of staff were kept, and ex-employees formed Red Triangle. A firm that would continue to support and maintain Alvis products to loyal owners, including parts, documentation, servicing and more. The Red Triangle eventually bought the rights to the Alvis car trademarks in 2009 and just recently, set to work on the ‘continuation series’.

“It was always a dream to be able to make cars again" said Red Triangle's Managing Director, Michael Hicks. "When the deal was negotiated, the incentive was it would only be right to produce new cars made by Alvis using the same parts and skills that were used in period.”

The continuation cars use Alvis chassis numbers and original drawings and are not only compliant to emissions legislation, but can also be entered into classic rallies. The prices for the new cars range between £300,000 to £350,000 depending on the specification.
I am guided by Michael, who at the back of a rough industrial estate opposite a gym and office building, pushes open these majestic green metal doors. Inside can only be described as an engineering haven for the Alvis aficionado.

The main workshop was a reserved, yet busy little space to explore. Most of the cars within were original, which included a couple of early 12/50s, a TA21 and even a 1939 Jensen S-Type in for a light mechanical overhaul. Peering over to the corner of this tiny workshop with The Rolling Stones playing in the backdrop, is a glorious 3 litre Graber coupe. Its bonnet is lifted, showing off modern components and a distinct lack of the usual SU carburettors. The interior is largely covered in plastic sheeting with some trim still yet to be applied. Whilst it looks like the one-of-three bodied in Switzerland, it was actually built this year and set to be delivered to a customer in Japan next year.
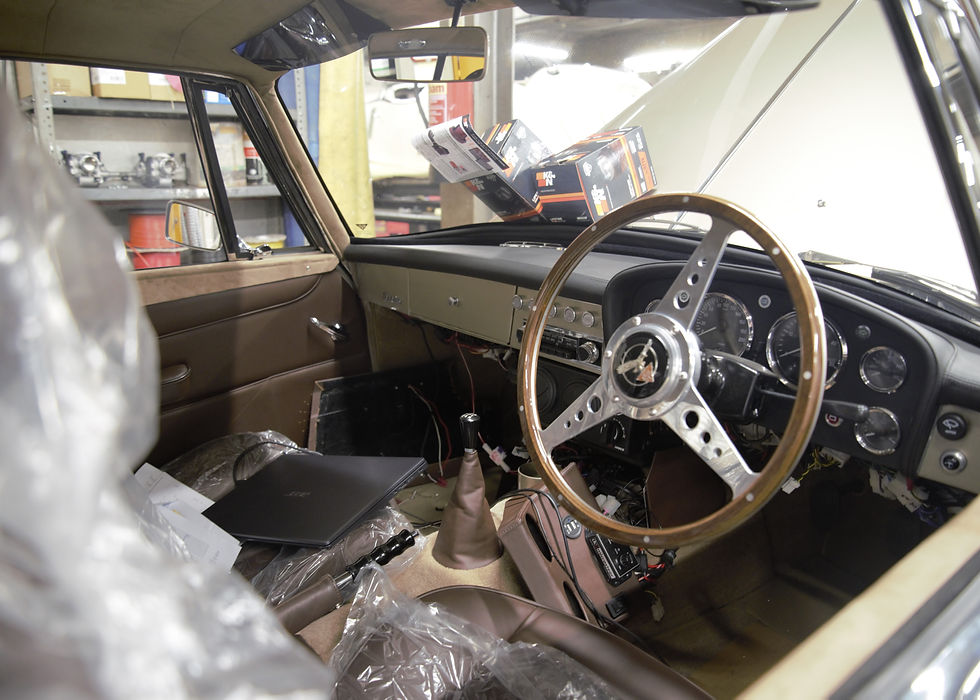
“So this is a brand new car, but it’s built on an original chassis. The chassis number classes it as an old car, but the rest is brand new built from stock parts that have been sitting on the shelf for 50 years.”
The 'new' Graber uses the basis of an original 3 litre Alvis engine, but the days of carburettor tuning are gone with electronic fuel injection and catalytic converters taking their place to meet emission targets. "Because the UK has a big industry for kit cars and low-volume manufacturers, we do have to go through approval, but not at the stringent levels that a bigger manufacturer would” said Michael.


Naturally with the engine upgrades, the continuation cars will produce a fair bit more oomph than the originals. "We would estimate about a 30-40hp increase over the original (Graber) engine. As for the gearboxes, we actually buy units from Tremec." The pre-war continuation cars receive a six-speed manual gearbox whereas post-war cars a five-speed, to which Michael says improve the drivability of the cars a "great deal.”

Directly opposite the Graber coupe, was the new convertible version on the ramp, ordered again by a customer in Japan. It was painted in primer and looked achingly majestic, overlooking the operations of the employees. That car is many stages away from eventually being finished, with remaining parts and testing still to be achieved. The rest of the cars there were original, which included a couple of early 12/50s, a TA21 and even a 1939 Jensen S-Type in for a light mechanical overhaul.
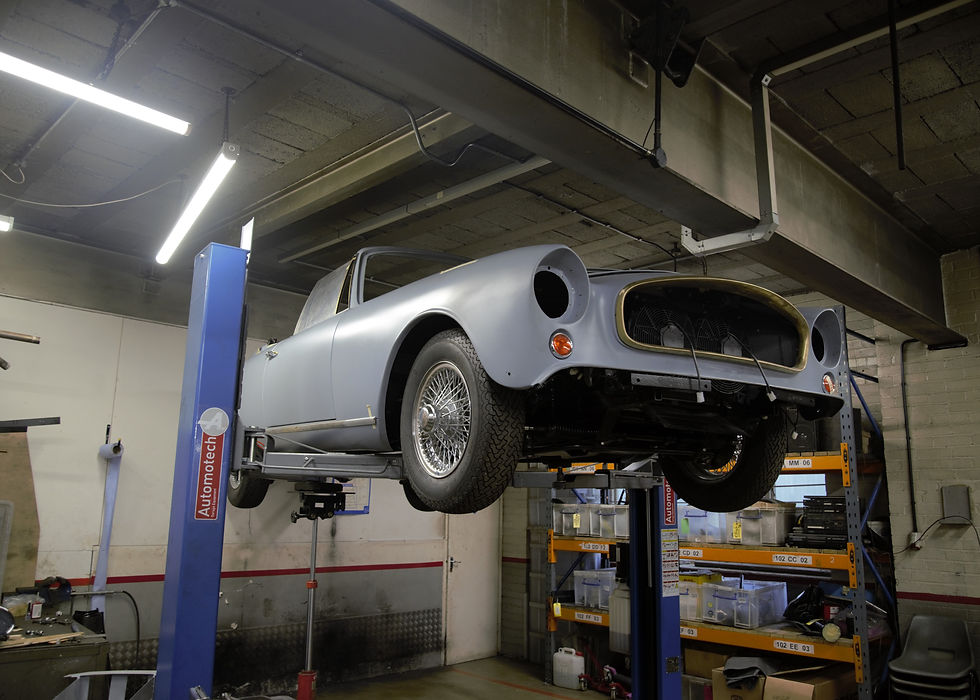
Next to that Jesnen was a door that revealed where the basis of the cars are constructed.
Immediately, I was taken by surprise. There are entire kitchen and living areas bigger than this. The entire room was taken by a wooden body buck for the Graber, a brand-new chassis for early 10/30 and half of a bare metal shell for a new Lancefield Drophead sitting opposite – also ordered by a customer in Japan. The entire room has the scent of sanded wood and fresh aluminium with tools on the side, including an English wheel to gradually shape the flat pieces of metal into bodywork.


Referring to panel specialist, Paul, "it's his job various pressures, making different angles and shapes for each panel. And naturally it takes time – hours and hours of pressing to eventually produce a shape. And then it’s applied to the ash frame and final adjustments take place.”
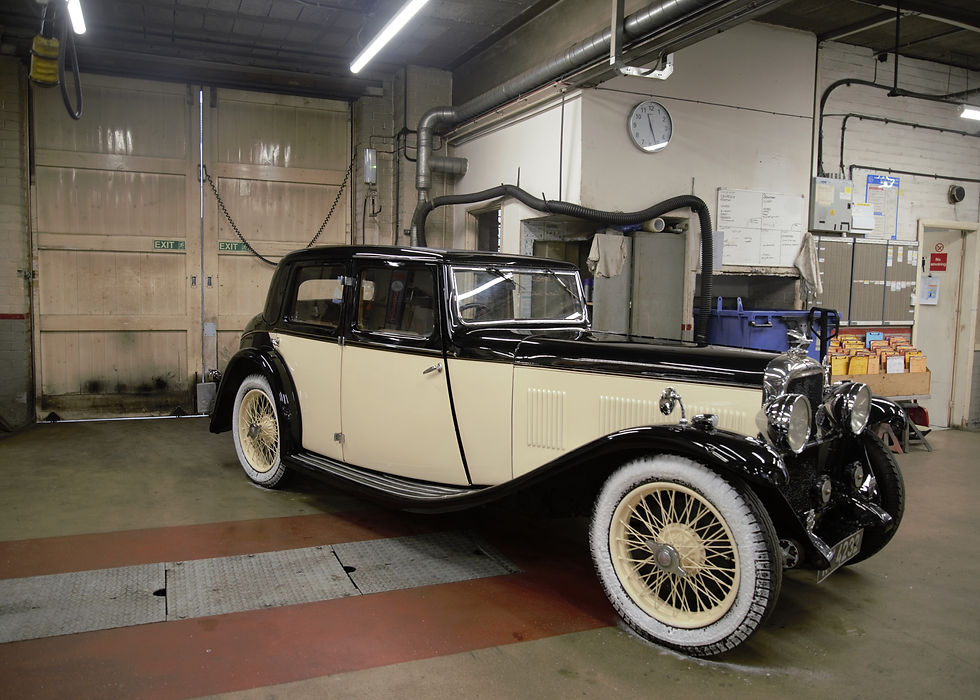
Michael tells me that each car takes several thousand hours to produce from base to finished product, and each individual part is handmade, using similar tools and the same skills from period. “We’re looking at about 18-months to 2 years for a build time of a car. We’re certainly not geared-up for going any quicker. So, that suits us and keeps the exclusivity of the cars.”

There is not a CAD machine in sight or anything remotely modern apart from a singular Apple Mac collecting dust in the corner, giving you the sense that these aren’t just small volume cars, they’re made by small volume staff as well.

Heading up a narrow set of stairs reveals an attic that would be worth more than its weight in gold. Scattered upon me is the entirety of Alvis’ parts stock which was kept since 1967. I stubbed my toe on an original 3 litre engine block that never found its way into a chassis, there were doors hanging above Michael’s head from some pre-war cars, and every gearbox, axle, bracket, clutch, sparkplug that you need for your Alvis, no matter which one, they have the right part for it up here. Sets of radiator grilles from Speed 20s were hung on the wall, should you ever need one.


Back downstairs was the restoration workshop, where a TE21 Drophead was being renovated for an American customer, as well as the original FWD Brooklands race car being prepared for paint. The straight eight monster is probably the hidden jewel of the tour, until Mike took us to the archive room sat just above the main dealership, which should never be ignored since no less than 20 cars, including an original Swiss-built Graber coupe and Lancefield Drophead sit proudly to lure in Kenilworth’s passers-by.

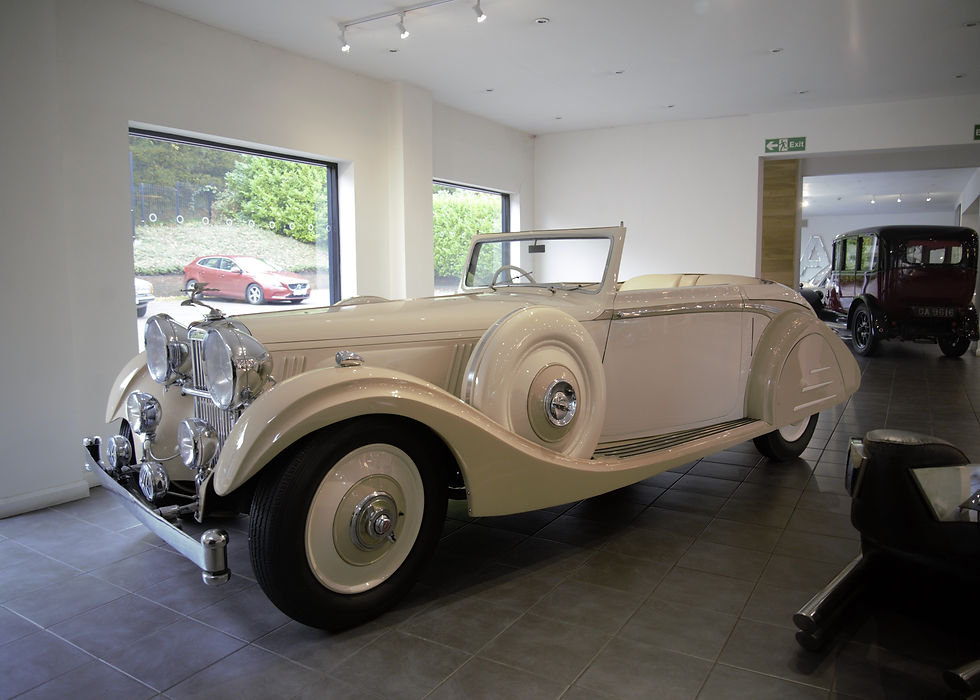
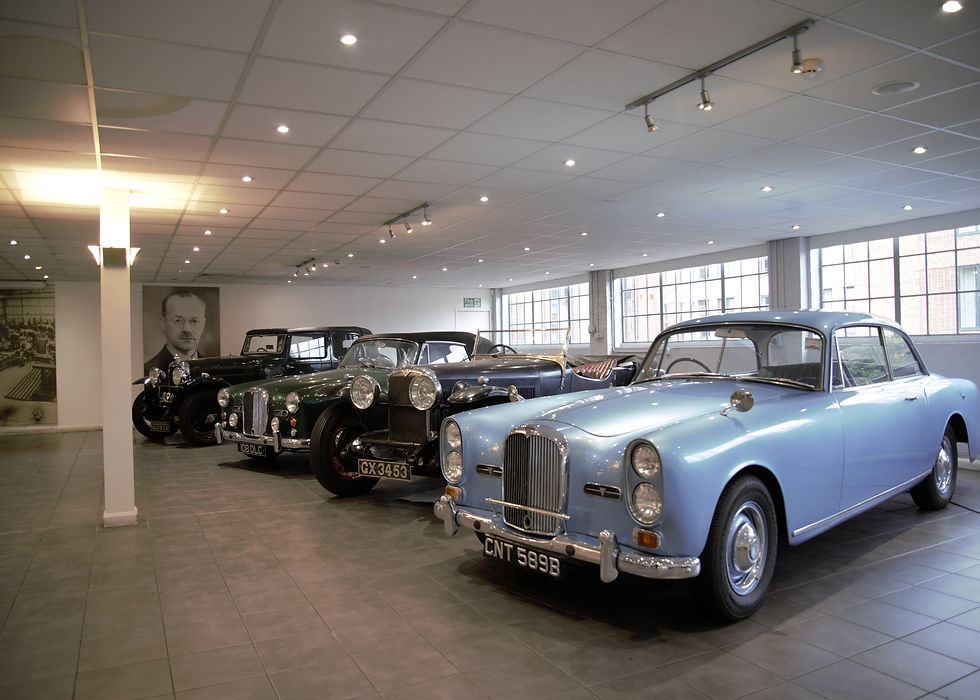
You can buy photocopies of an Alvis car’s letters of correspondence and communication. You name a chassis number; they’ve probably got a thick paper record of it somewhere. Michael explained how customers could do this while gently brushing over correspondence to Alvis from the late Duke of Edinburgh, citing gearbox issues with his tailored TD21 Drophead. Not to mention invoices and receipts to fighter ace, Douglas Bader regarding work to his car.
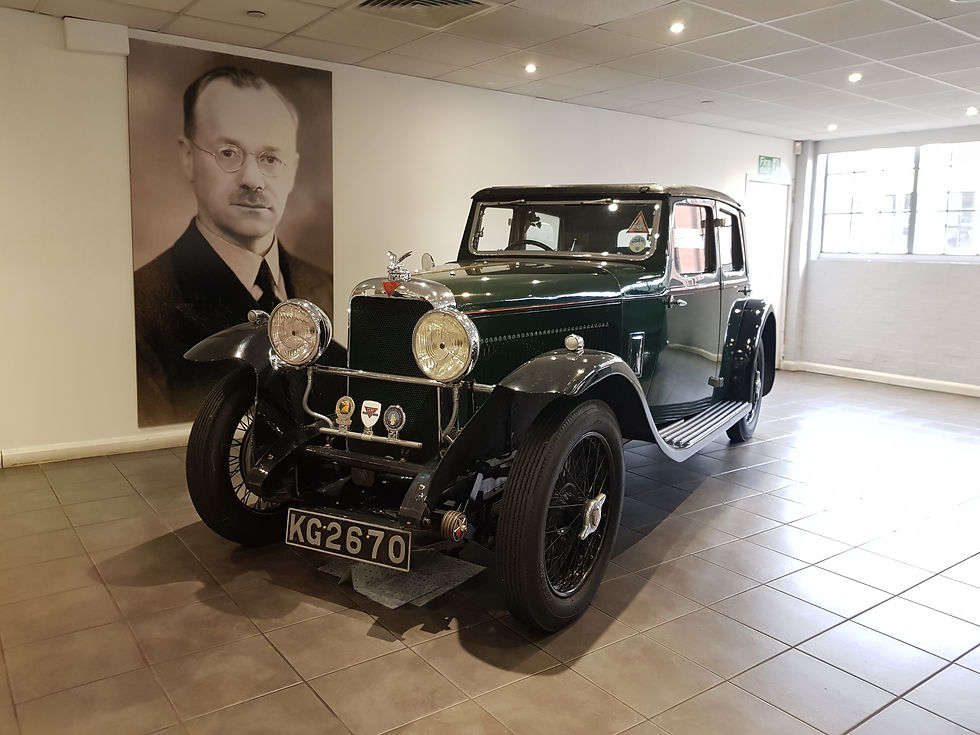
The industry of reproducing classic cars has seen somewhat of a surge in popularity within the last several years. From restomods to brand-built continuation models, it seems the way forwards is backwards. But whereas Jaguar, Aston Martin and Bentley charge millions for continuation products, suddenly 300 grand on a new Alvis seems like great value - especially when you consider they're as original as you can get while meeting modern regulations.
Comments